Isolamento termico

L’isolamento termico contribuisce a ridurre la dispersione d’energia attraverso l’involucro edilizio, e ogni tipo di edificio o applicazione richiede una specifica soluzione tecnica .
Soprema, grazie alla sua consolidata esperienza pluriennale nella progettazione e produzione di prodotti per l’impermeabilizzazione e per l’isolamento termico ed acustico, è in grado di supportare adeguatamente sia il progettista, sia l’utilizzatore nella scelta di soluzioni ad alte prestazioni .
Tra gli isolanti oggi più diffusi ed utilizzati sul mercato si annoverano il polistirene estruso (XPS) , il polistirene espanso (EPS), il poliuretano espanso (PIR) e la lana di roccia (MW). Questi materiali altamente prestazionali rappresentano soluzioni isolanti di assoluto valore per ogni tipo di partizione, quali, tetti piani e inclinati, pareti, soffitti e pavimenti.
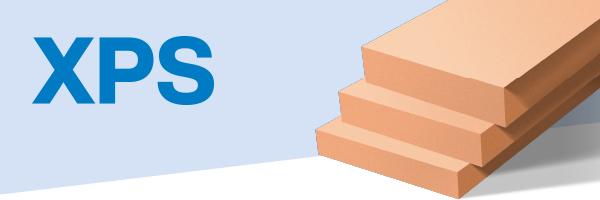
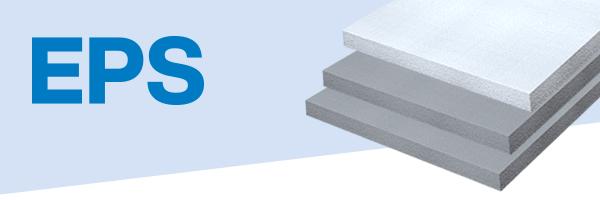
XPS
Gli isolanti in polistirene estruso XPS sono prodotti mediante l’impiego di granuli di polistirene, diversi additivi e gas espandenti. Il polistirene viene stoccato in silos e, attraverso il sistema di alimentazione, viene mescolato al resto degli additivi con l’aggiunta di eventuali coloranti, che danno al prodotto finale un colore caratteristico. La miscela di polistirene e additivi viene immessa in un estrusore che per effetto dell'aumento della temperatura e della pressione, si fonde in una massa fluida. All'uscita dall'estrusore, il passaggio repentino alla pressione atmosferica produce la gassificazione dell'agente schiumogeno (gas espandente), consentendo la formazione della schiuma e quindi di una lastra solida. Prima di poter essere lavorate, le lastre vengono stabilizzate e poi trasferite alla fase di fresatura dei bordi perimetrali e quindi all’imballaggio finale, pronto per la spedizione sul mercato.
L’XPS è impiegato soprattutto per l’isolamento termico di ambienti particolarmente umidi sottoposti a elevate sollecitazioni meccaniche.
Le peculiarità distintive della gamma XPS infatti, sono, da un lato la sua struttura a celle chiuse e la pelle di estrusione che garantiscono un basso, quasi nullo, assorbimento di acqua e umidità, e dall’altro garantire alte prestazioni meccaniche, fondamentali per l’utilizzo in partizioni edilizie su cui gravano alti carichi meccanici alla compressione come, terrazze con destinazione parking, sottopavimenti industriali, celle frigorifere, fondazioni sottoterra, massicciate ferroviarie ecc. La resistenza meccanica varia da 300 a 500 fino a 700 kPa.
Le applicazioni tipiche dell’XPS, sono:
- Tetti piani con stratigrafie a tetto rovescio
- Tetti piani con destinazione a parcheggio
- Sottopavimenti civili ed industriali
- Sottotegola con stratigrafia a tetto sarking (listellatura e assito)
- Intercapedini
- Pannelli sandwich
I vantaggi dell’XPS sono così riassumibili:
- Alte prestazioni meccaniche da 300 a 700 kPa
- Alti valori di isolamento termico con valori di Conducibilità da 32 a 34 mmW
- Basso impatto ambientale perché prodotto secondo i principi dell’economia circolare
- Conforme ai Criteri Ambientali Minimi (CAM)
- Riciclabile al 100% a fine vita
- Corredato da Certificazioni Ambientali (EPD/LCA)
EPS
Il polistirene espanso sinterizzato (EPS) è una delle forme più importanti in cui viene impiegato il Polistirene (l’XPS e l’EPS sono due materiali espansi stirenici, ma caratterizzati da processi produttivi differenti).
Il processo produttivo dell’EPS sostanzialmente si può sintetizzare in 3 fasi: la pre-espansione, la stagionatura e lo stampaggio, per i manufatti finiti stampati o il taglio a fili oscillanti per i pannelli.
Pre-espansione
Le perle di Ps espandibile vengono pre-espanse, generalmente per mezzo di vapore a temperatura superiore a 90 °C, nel cosiddetto pre- espansore. In questo le perle, a seguito della vaporizzazione dell’agente espandente, si rigonfiano fino a 20-50 volte il loro volume iniziale.
In questo processo si forma, all’interno delle perle, una struttura a celle chiuse, fondamentale per il successivo impiego come isolamento termico. Il grado di espansione, che dipende essenzialmente dalla durata del trattamento termico nel pre-espansore, determina la massa volumica apparente dei manufatti e quindi tutte le loro caratteristiche fisiche.
Stagionatura o Maturazione
Le perle pre-espanse devono stazionare un certo tempo in sili arieggiati. Con il raffreddamento i residui di espandente e di vapore acqueo condensano nelle singole celle. La depressione che così si forma viene annullata dall’aria che si diffonde all’interno delle celle; in questo modo le perle pre-espanse raggiungono la stabilità necessaria per le fasi successive.
Stampaggio
Le blocchiere, costituite da forme parallelepipede in metallo, provviste di fori di entrata per il vapore su tutti i lati, vengono riempite di perle pre-espanse e sottoposte di nuovo all’azione del vapore saturo; si raggiungono temperature di 110-120 °C, le perle si rigonfiano ulteriormente e, diventate appiccicose, si saldano tra di loro (“sinterizzano”) per effetto della loro pressione interna, fino a formare un blocco omogeneo di espanso. Dopo un breve periodo di raffreddamento, i blocchi vengono sformati e messi in deposito per un periodo variabile da alcuni giorni a due mesi, durante il quale raggiungono la stabilità necessaria per le diverse applicazioni. Di qui vengono prelevati per il taglio in lastre, che avviene con seghe a nastro o a filo caldo e per eventuali altre operazioni meccaniche, come sagomature dei bordi, ottenute per fresatura.
Stampaggio di lastre e altri manufatti
Il processo è lo stesso descritto per i blocchi, ma le lastre vengono stampate singolarmente in apposite macchine automatiche (presse con lo stampo avente le forma dell’articolo che si vuole ottenere). Si ha il vantaggio di ottenere direttamente la forma desiderata, senza ulteriori lavorazioni meccaniche: ciò è particolarmente utile per le forme non piane (p.es. sottotegole, lastre con contorni sagomati, cassonetti, lastre con superficie decorata a rilievo, coppelle).
Grazie alla continua ricerca e sviluppo fatta dalle più importanti industrie che operano nei vari Paesi ed alla consolidata affidabilità nel tempo, attestata anche dai più importanti Laboratori di controllo e Enti di Certificazione Internazionali, i prodotti in EPS hanno una larga diffusione nelle varie applicazioni, quali:
- Rivestimenti a cappotto
- Sottotegola
- Tetti piani con impermeabilizzazione con membrane sintetiche in Pcv/Tpo
- Intercapedini
- Riscaldamento in sottopavimenti
con importanti vantaggi, così riassunti:
- Elevato isolamento termico con valori di conducibilità da 29 a 35 mmW.
- Alte prestazioni meccaniche
- Elevata stabilità dimensionale nel tempo
- Conformità ai Criteri Ambientali Minimi (CAM)
- Basso impatto ambientale perché prodotto secondo i principi dell’economia circolare
- Corredato da Dichiarazioni Ambientali: EPD/LCA
- Riciclabile al 100% a fine vita
- Facile lavorabilità in cantiere

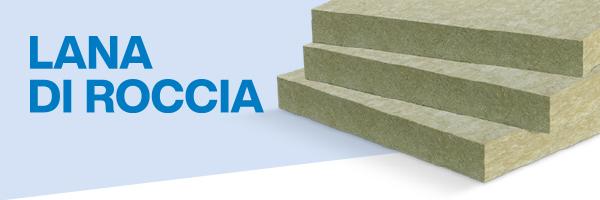
PIR
Il poliuretano espanso rigido (PIR) è un polimero reticolato termoindurente che nasce dalla reazione di due componenti principali - polioli e poliisocianati, in presenza di un agente espandente e di altri additivi. Nel corso della reazione, che porta le materie prime dallo stato liquido a quello solido del polimero finale, la schiuma garantisce una forte adesione a quasi tutti i tipi di supporti sia rigidi che flessibili, come ad esempio film di alluminio, velo vetro bitumato, tessuti in velo vetro saturato o mineralizzato ecc..
Grazie all’utilizzo di questi rivestimenti protettivi, i prodotti in PIR trovano ampio spazio nell’isolamento termico di qualsiasi tipologia di struttura edilizia sia verticale che piana o inclinata, quali:
- Tetti piani con impermeabilizzazione con membrane bituminose e sintetiche in Pvc e Tpo
- Sottotegola
- Rivestimento a cappotto
- Isolamento in intercapedini
I punti di forza degli isolanti in PIR:
- Elevati valori di isolamento termico (Coducibilità da 22 mmW a 28 mmW)
- Ampia gamma di applicazioni grazie alla presenza di rivestimenti bifacciali
- Conformità ai Criteri Ambientali Minimi (CAM)
- Basso impatto ambientale perché prodotto secondo i principi dell’economia circolare
- Corredato da Certificazioni Ambientali EPD/LCA
- Facile lavorabilità in cantiere
Lana di Roccia
La lana di roccia è ottenuta da materiale roccioso presente in grandi quantità in natura. E' un materiale isolante costituito da fibre ricavate attraverso un processo di fusione da rocce di tipo basaltico. Le porzioni di rocce vengono frantumate e unite a calcare e minerali. Il calcare è utile per abbassare la temperatura di fusione della roccia, mentre i minerali servono a calibrare la qualità del materiale finale;
Il materiale ottenuto viene depositato in apposito forno in cui, avviene la sua fusione ad una temperatura di ca. 1500 °C; successivamente alla fase di fusione, il materiale viene trasformato in fibre minerali che, dopo uno specifico trattamento mediante resine e olio e passaggio in un forno di polimerizzazione e solidificazione dei leganti, si formano i pannelli pronti per la fase di taglio a misura e imballo finale.
Oltre alla funzione termoisolante, la lana di roccia offre vantaggi soprattutto per la protezione antincendio. La lana di roccia non brucia e presenta un punto di fusione di oltre 1000 °C, caratteristica che in caso d’emergenza è in grado di contenere o prevenire la propagazione dell’incendio.
Inoltre la lana di roccia è idrorepellente, resistente all’invecchiamento, durevole e presenta buone caratteristiche fonoassorbenti. È anche resistente alla putrefazione, ai parassiti e ai funghi.
È adatta per isolare tetti piani e inclinati, ma può essere utilizzata anche come isolante trasversale sopra, sotto e tra le travi; viene impiegata anche per la coibentazione dove sono richiesti requisiti antincendio o per isolare le travi d’acciaio non resistenti al fuoco.
La stabilità dimensionale dei pannelli isolanti in lana di roccia è efficace in particolare nelle facciate retroventilate, esposte a elevata escursione termica.
I punti di forza degli isolanti in Lana di roccia (MW)
- Classificazione al fuoco in Euroclasse A1
- Alte prestazioni di isolamento acustico
- Buona stabilità dimensionale
- Buone prestazioni termiche
- Conformità ai Criteri Ambientali Minimi (CAM)
- Corredata da Certificazione EUCEB
Le principali applicazioni degli isolanti in Lana di roccia (MW)
- Tetti piani con impermeabilizzazione con membrane sintetiche in Pvc/Tpo
- Isolamento acustico di pareti divisorie
- Rivestimento a cappotto
- Isolamento in intercapedini con tamponamento con lastre di Cartongesso
- Controsoffitti a vista
- Sottotetti in controsoffittatura

Hai una domanda?
Il nostro servizio tecnico e commerciale è a tua disposizione per rispondere alle tue domande.